With integrated and customised concepts in the field of catalytics, condensation and combined processes, Standardkessel Baumgarte develops technologically high-quality solutions for emission reduction and pollutant abatement.
Denitrification (DeNOx)
The efficient reduction of nitrogen oxides is becoming more and more important. According to the new emission guidelines (BREF/BAT), stricter limit values apply. By combining primary and secondary measures, nitrogen oxide emissions can be efficiently limited. Standardkessel Baumgarte GmbH acts as an EPC for the entire value chain. Tailor-made solutions for combustion optimisation, selective non-catalytic reduction (SNCR) and selective catalytic reduction (SCR), or combinations of these processes, are realised according to customer requirements.
Selective Catalytic Reduction (SCR)
The Selective Catalytic Reduction (SCR) process is mainly chosen when there is a high nitrogen oxide content in the exhaust gas/flue gas/exhaust air and to comply with the new BREF emission limits. The nitrogen oxides react in an oxidising atmosphere in the presence of a reducing agent to form molecular nitrogen and water. For this purpose, the reducing agent ammonia or an ammonia-splitting reducing agent (ammonia water or urea) is injected into the duct and homogenously distributed before the catalytic converter. Catalytic materials lower the activation energy of the chemical reaction so that the required NOx reduction can take place at low temperatures. Depending on the application, honeycomb or plate catalysts with different channel openings and activities are used for denitrification. The operating temperature depends on the location of the installation of the catalyst (high dust, low dust, tail-end) and the flue gas composition.
Static mixers are installed to optimise the temperature, NOx/NH3 and velocity distribution upstream of the catalyst. Therefore NH3 slip, possible plugging and corrosion are minimised.
Reducing agent may be injected by the following two variants. Variant one uses pre-evaporation via spray or contact evaporators. In this case, the reducing agent (NH3 or NH4OH) is first converted into the gaseous phase by means of an evaporator and introduced into the flue gas duct with air or flue gas via a so-called "injection grid" (distributor pipes/AIG). The second variant is direct injection. Here, the reducing agent is injected directly into the duct via special lances and evaporated by the flue gas.
Catalytic oxidation (CatOx)
The catalytic process is ideal for exhaust gas and exhaust air purification. The catalytic converter enables the conversion of pollutant gases, especially volatile organic compounds (VOC), into environmentally compatible substances.
Catalytic processes are generally characterised by lower reaction temperatures than comparable thermal processes. This enables more efficient process control with significantly reduced energy input. The catalytic process is exothermal. Depending on the application and the level of pollutant loading, heat is recovered recuperatively or regeneratively.
Depending on the pollutant concentration in the exhaust gas and the exhaust air, two technologies of catalytic exhaust air purification are available. For applications with medium to high concentrations, Standardkessel Baumgarte use systems with recuperative heat recovery (CatOx). For applications with low to medium concentrations, we use systems with regenerative heat recovery (RCO). Both technologies are designed for purification levels of 99% or higher.
Catalytic oxidation with recuperative heat recovery (CatOx)
The process of catalytic oxidation with recuperative heat recovery uses gas-gas heat exchangers to achieve the desired temperature for catalytic oxidation. Depending on the VOC or pollutant concentration, an energy input is required. With the use of a highly efficient heat exchanger, autothermal operation through heat recovery is possible even at low VOC or pollutant concentrations. The use of recuperative heat recovery ensures a reliable separation of exhaust air and clean air.
The CatOx technology can be used for applications on processes up to 25 bar, as well as, for the cleaning of oxygen-deficient gases.
Catalytic oxidation with regenerative heat recovery (RCO)
The regenerative heat recovery catalytic oxidation process uses one or more beds of heat absorbing material for regenerative heat exchange and is able to operate without energy input even at low VOC or pollutant concentrations, unlike the CatOx process.
Catalytic oxidation after condensation (combined process)
There are a number of processes and plants (examples are: tank farms, decanting processes, reactions in the chemical industry) that emit waste gas/exhaust air containing pollutants or solvents with different volume flows, with high and low concentrations and with interruptions in time. The requirements for a cleaning process are complex and require the use of a multi-stage cleaning process for ecologically sensible cleaning.
A typical combination is direct deep-freeze condensation (bath cooler or spray cooler) followed by catalytic oxidation. This multi-stage process has become more and more important and offers an economically flexible solution for waste gas/exhaust air purification.
The exhaust gas or exhaust air is directly condensed to reduce and equalise the concentration of pollutants and solvents. To achieve the emission limits, the pre-cleaned exhaust gas/exhaust air is treated in the second stage in a catalytic oxidiser with recuperative heat recovery.
The combination described is capable of solving a wide variety of tasks. On the one hand, the first stage, designed as a condenser, provides pre-cleaning and solvent recovery; on the other hand, condensation reduces concentration peaks and fills concentration valleys. This allows energy-optimised process control of the downstream catalytic oxidation.
Combination of denitrification and catalytic oxidation
Purification of volatile organic compounds and nitrogen oxides by combining both catalytic processes.
Condensation
Standardkessel Baumgarte has the necessary know-how to develop an optimal concept for emission reduction, recovery and flue gas conditioning that is specifically tailored to your requirements.
A suitable process for separating pollutants or solvents from a carrier gas is direct condensation, in application under normal pressure conditions as well as in the positive and negative pressure range.
Two technologies are available for direct condensation for this purpose.
Spray cooler
In the spray cooler the waste gas is cooled by direct contact with the cooled liquid in the liquid jet. The liquid itself is adjusted to the desired temperature by indirect cooling, usually in a heat exchanger.
As a result of the continuous supply of liquid, the phase interface between gas and liquid is constantly renewed. The intensive contact causes a washing, absorption or condensation effect and, thus, a mass transfer between gas and liquid. The exhaust gas cools down to condensation temperature, the pollutants and solvents contained in the exhaust gas condense to saturation conditions. The condensate mixes with the supplied liquid and is collected together with the spray jet in the apparatus sump. The liquid is drained off via a level control and the purified gas stream is discharged via a specially designed demister.
If required, the condensation unit can also be designed for operation on discontinuous processes (batch operations) and in the event of fluctuations in the exhaust gas volume. The technology is often used as a pre-separator or quencher for highly loaded or very warm exhaust gas streams as a preliminary stage of further cleaning processes and is also applicable for use in closed exhaust gas systems (e.g. of a dryer or coating system).
Bath cooler
For condensation of the components, the exhaust gas is conveyed by means of a blower in a bubble column through the liquid bath, which is cooled to the condensation temperature. The liquid usually corresponds to the composition of the condensate from the exhaust gas stream. The exhaust gas cools in the bubble column to the temperature set in the accumulator below the dew point of the compounds. In the process, the pollutants and solvents contained in the exhaust gas condense out to saturation conditions. The condensate is collected directly in the liquid. If required, the system can be designed for operation in discontinuous processes (batch processes).
As the cooling process of the waste gas is achieved by direct contact with the liquid bath, the bath itself is adjusted to the desired temperature by indirect cooling. Due to the turbulence generated by the exhaust gas streaming through, no plugging/clogging can occur. In this way, the bath cooler constantly cleans itself. Between the exhaust gas mixture and the cooled liquid, there are no separating transfer walls that are prone to fouling. The process is also successfully used when concentration peaks require smoothing in order to make other downstream recoveries and cleaning processes possible at all. The outlet concentration remains almost the same.
Combined processes
The demands of industry on cleaning processes are complex, requiring system solutions and consideration of the individual possible emission reduction measures.
In many cases, waste gas and exhaust air streams can no longer be purified in an ecologically sensible way using a single-stage purification process alone.
Operational experience has shown that, with regard to the constituents and their concentration in the exhaust gas, further process stages usually have to be used upstream and/or downstream as supplements. Official regulations also often demand that process combinations be provided as a complete solution. Combined processes are multi-stage systems in which an adapted process is used for each stage, depending on the volume flow and the pollutant load.
Two-stage condensation
Processes frequently emit waste gas streams with pollutants or solvents of the most varied properties, which have to be considered when condensation is applied.
These include, for example, the pour point undershooting of individual substances and mixed crystals (eutectic), insolubilities or a freezing out of substances from the liquid due to partial solubility. If a single-stage deep-freeze condensation is not sufficient, a pre-condensation stage is installed upstream. The stage is designed according to the required temperature control for condensation.
A typical application is the combination of the spray cooler with the bath cooler. In this case, the spray cooler is used as a pre-separator or as a quencher, for example, in the case of a highly charged, very warm exhaust gas stream or a high water content in the exhaust gas. The pre-condensation is then usually operated at condensation temperatures above 0 °C, the second stage in the low-temperature range. The temperature control, i.e. the selected temperature grading, must be determined for optimum process control depending on the application.
Further processes by combining the cleaning processes with
- Upstream/downstream gas scrubbing for the separation of inorganic pollutants, etc.
- For waste gas streams with short concentration peaks, there is the possibility of using an adsorbent bed to smooth concentration peaks before catalytic oxidation.
- Use of zeolites for concentration for optimised design of downstream catalytic oxidation
"The purification of waste gases and process gases is increasingly becoming a core issue in the design of plants due to the increasing environmental requirements. With our processes, we can not only clean the gases, but also make the ingredients available for recycling."
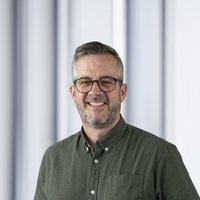
Olover Pettersson
Head of Gas Cleaning