THE TASK
For the production of pharma packaging material, a pharmaceutical company planned a new production facility at the East Coast, USA. Standardkessel Baumgarte GmbH`s catalytics division was entrusted with the delivery of a catalytic exhaust air cleaning system. This is designed to remove the volatile organic compounds from the exhaust air in a safe and environmentally friendly manner. This will enable the plant to meet the customers environmental protection requirements and ensure that no polluted exhaust air is released into the environment. The system is designed for an exhaust air volume flow of 6700 Nm3/h.
THE SOLUTION
By the use of a catalyst, the required oxidation temperature for the conversion of the organic compounds is lower than with thermal oxidation. The catalytic reaction releases thermal energy during oxidation. By using a highly efficient heat exchanger, autothermic operation is already possible at low VOC concentrations. Heat recovery takes place recuperatively in order to ensure safe and reliable separation of exhaust air and clean air. The optimized controls ensure operation in a large turn-down range and at various VOC concentrations without supplementary energy.
With the suggested process and the quality standards applied, all of the customer-specific demands can be met, including calorific efficiency and availability.
For more information, please see our reference sheet.
"The purification of waste gases and process gases is increasingly becoming a core issue in the design of plants due to the increasing environmental requirements. With our processes, we can not only clean the gases, but also make the ingredients available for recycling."
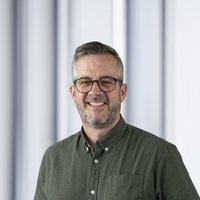
Olover Pettersson
Head of Gas Cleaning
Technical Data
1
6,700 m³/h i. N.
min20 °C
max60 °C
VOC - max.60 kg/h
MIBK, Aceton
VOC20 mgC/m³ i. N.
3 g/m³ i. N.
Installed350 KW
atmospheric
continuous
2020